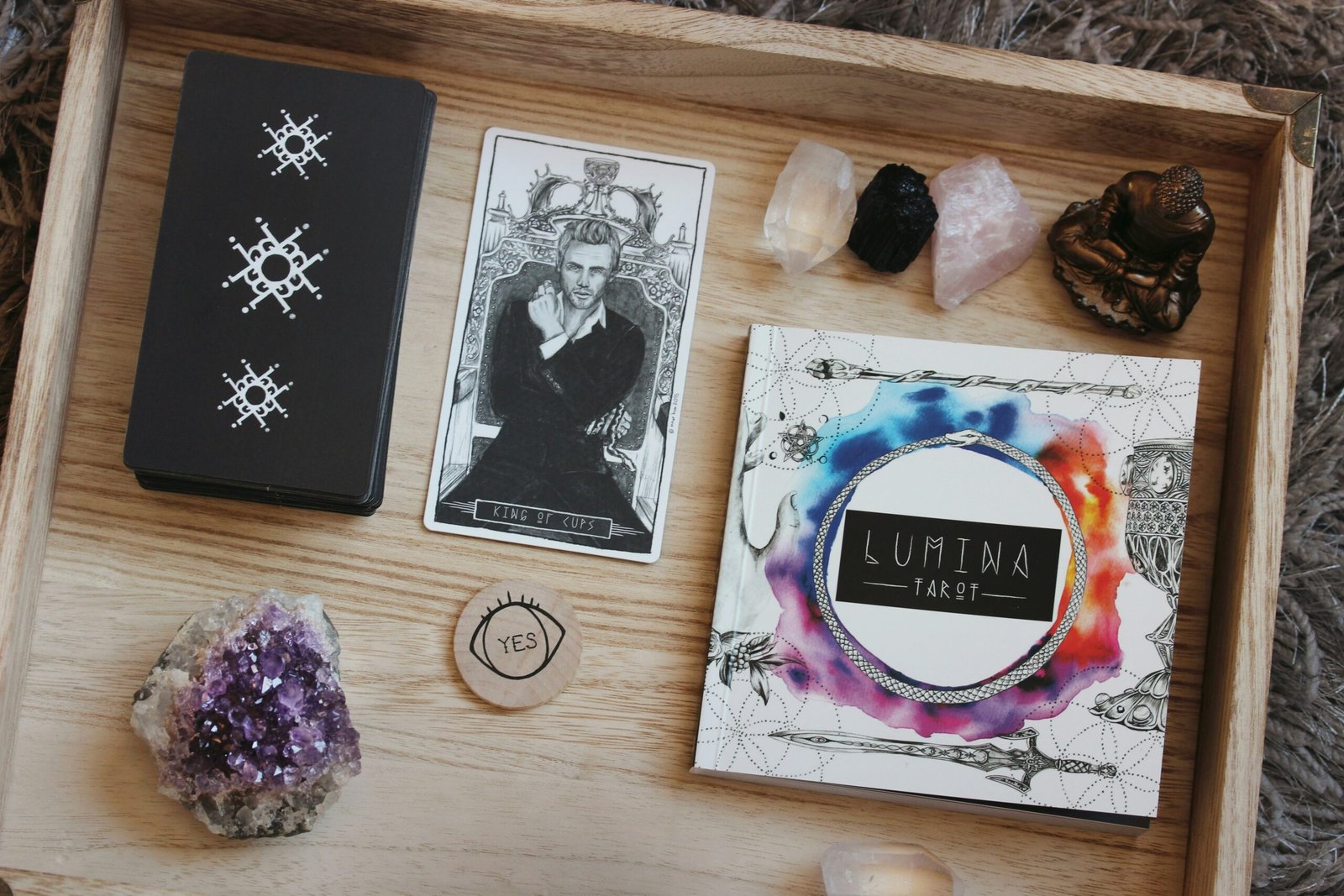
The Importance of Windchill Reliability Prediction for Engineering Executives
Introduction to Windchill Reliability Prediction
Windchill Reliability Prediction is a sophisticated tool utilized within engineering and product lifecycle management to assess and enhance product reliability. It serves a crucial purpose in helping organizations forecast potential failures and maintain high standards of quality throughout the product development process. By implementing advanced algorithms and historical data, Windchill allows engineering executives to make informed decisions that directly impact product performance and longevity.
This predictive technology operates on the foundation of reliability engineering principles, which aim to ensure that products perform their intended functions without failure for a specified duration. Windchill Reliability Prediction combines engineering data with statistical analysis to generate reliability metrics, enabling stakeholders to evaluate the performance of components before they are fully fabricated or deployed.
As part of the broader framework of engineering and product lifecycle management, Windchill Reliability Prediction integrates seamlessly with other software solutions that address design, development, and production aspects. This integration facilitates a holistic view of the product lifecycle, allowing engineering executives to engage in proactive risk management and strategic planning. The insights provided by this tool are vital in optimizing product design, leading to enhanced customer satisfaction and reduced warranty claims.
Moreover, with the rise of complex engineering systems, the need for reliable assessments has become increasingly pertinent. Windchill Reliability Prediction stands at the forefront of addressing these challenges by offering a structured approach to predict reliability outcomes. By leveraging this advanced technology, engineering executives can ensure that their products not only meet the market demands but also adhere to stringent safety and regulatory requirements.
Understanding Reliability in Engineering
Reliability in engineering refers to the probability that a product or system will perform its intended function under specified conditions for a defined period. This concept is crucial for engineering executives, as it directly impacts product quality, customer satisfaction, and ultimately, the company’s reputation. A reliable product minimizes the chances of failure, ensuring that it satisfies user expectations consistently.
Several key factors contribute to a product’s reliability. First, the design phase plays a pivotal role. A well-thought-out design that considers potential stressors, user environments, and operational demands can significantly enhance reliability. Engineers must anticipate how various components will interact and withstand real-world conditions. This proactive approach is essential in developing robust products that meet performance standards.
Materials selection is another critical factor affecting reliability. The quality and characteristics of materials influence how a product endures environmental factors such as temperature fluctuations, moisture, and mechanical stress. Choosing materials with high durability and resistance to wear can enhance the lifespan of the product. Additionally, understanding material properties and their behavior under different circumstances is vital for ensuring that a product meets its reliability objectives.
Manufacturing processes also play a significant role in ensuring the reliability of engineering products. Consistency in production methods, as well as adherence to stringent quality control measures, can lead to a reduction in defects and variations. Variability in the manufacturing process can directly affect reliability, so it is essential to implement rigorous testing and validation procedures to identify potential issues before products reach the market.
By comprehensively understanding these factors—design, materials, and manufacturing—engineering executives can foster a culture of reliability within their organizations, leading to enhanced product performance and customer trust.
Challenges Faced by Engineering Executives
Engineering executives play a critical role in ensuring the reliability of products, yet they continually encounter several challenges that can impede their efforts. One prominent issue is time constraints. In today’s fast-paced market, the demand for rapid product development often overrides the need for thorough testing and reliability assessments. As a result, engineering teams may feel compelled to prioritize quick releases over meticulous reliability evaluations, which can ultimately affect the product’s long-term performance and safety.
Resource allocation also presents a significant challenge. Engineering executives must judiciously distribute limited resources across various projects, balancing the immediate needs of product development with investments in reliability improvement initiatives. This often leads to difficult decisions, as some projects may not receive the attention or budget necessary to ensure optimal reliability outcomes. Insufficient resources can result in increased product failure rates, thereby damaging consumer trust and impacting the organization’s bottom line.
In addition to these challenges, effective communication between teams is crucial yet often lacking. Engineering executives oversee various departments, including design, manufacturing, quality assurance, and marketing. A breakdown in communication among these teams can lead to misalignment in product goals, which may compromise reliability. Elderly systems or processes might exacerbate these communication gaps, resulting in siloed information that hampers collaborative problem-solving efforts.
Finally, evolving customer expectations contribute to the complexity of maintaining product reliability. Today’s consumers demand not only high-quality products but also advanced features and longer-lasting performance. As customer preferences shift, engineering executives must remain agile and responsive to these expectations while ensuring that reliability is not sacrificed in the pursuit of innovation. Developing a robust strategy for windchill reliability prediction can play an essential role in addressing these challenges, enabling the organization to meet market demands without compromising product integrity.
The Role of Data in Predicting Reliability
In the domain of engineering, the significance of data collection and analysis cannot be overstated, particularly when it comes to predicting product reliability. Engineering executives rely heavily on precise reliability predictions to make informed decisions regarding product development, enhancement, and lifecycle management. Data serves as the backbone of these predictions, offering insights that help in assessing the long-term performance of products under various conditions, such as windchill effects.
To effectively predict reliability, several types of data are essential. First, historical failure data provides a foundation for understanding how similar products have performed under comparable circumstances. This historical perspective allows engineers to identify patterns and potential failure modes, leading to a more reliable product design. Furthermore, environmental data, including temperature and humidity levels, is crucial for assessing the reliability of products in varying conditions. Specifically, understanding windchill factors can aid in recognizing how environmental stresses may affect material integrity and operational efficacy.
Additionally, real-time data collection through advanced monitoring systems can significantly enhance reliability predictions. Technology such as Internet of Things (IoT) sensors captures data on product performance during actual usage. This continuous stream of data enables engineering executives to swiftly identify issues before they escalate into major failures, fostering a preventative rather than reactive approach to product management.
The integration of predictive analytics tools also bolsters data-driven decision-making. By utilizing statistical models and machine learning algorithms, executives can analyze large datasets to derive actionable insights. These insights can lead to improvements in design, material selection, and overall product reliability. Ultimately, the effective use of data allows engineering teams to not only predict reliability but also instills a culture of continuous improvement, ensuring that the end products meet or exceed market expectations.
Benefits of Utilizing Windchill Reliability Prediction
Windchill Reliability Prediction offers numerous advantages that are particularly beneficial for engineering executives aiming to enhance operational efficiency and product performance. One of the primary benefits is the significant reduction in time to market. By employing predictive reliability analyses early in the product development lifecycle, engineering teams can identify potential failure modes and address them promptly. This proactive approach minimizes delays often associated with unforeseen issues, allowing companies to introduce their products to the market swiftly and more efficiently.
Moreover, using Windchill Reliability Prediction fosters improvements in product quality. Advanced analytics provided by this tool enable teams to scrutinize and optimize designs, leading to more robust and reliable products. Enhanced quality assurance processes contribute to increased customer satisfaction, which is a critical factor for sustaining competitive advantage. As engineering executives prioritize the delivery of high-quality products, the reliability prediction capabilities become invaluable assets in achieving this goal.
Additionally, Windchill Reliability Prediction significantly decreases the risk of failures throughout a product’s life cycle. By identifying reliability concerns during the design phase, organizations can implement corrective measures before production, thus reducing warranty claims and improving overall product dependability. This predictive capability helps establish a more resilient product line, which ultimately enhances brand reputation and trust in the marketplace.
Lastly, enhanced collaboration is another notable benefit. Windchill Reliability Prediction serves as a centralized platform where cross-functional teams can share insights and data effectively. By breaking down silos and fostering communication among different departments, this platform empowers engineering executives to make informed decisions based on comprehensive data, ultimately driving innovation and continuous improvement.
Case Studies: Success Stories of Windchill Implementation
Organizations across various industries have successfully utilized Windchill Reliability Prediction to enhance their product development processes, leading to increased efficiency and reduced costs. One notable case is that of a leading aerospace manufacturer, which faced challenges in managing vast amounts of data related to product design and lifecycle management. By implementing Windchill, the company was able to create a centralized repository for all engineering data, improving accessibility for their teams. The result was a marked reduction in development time and an increase in product reliability, with the company reporting a 25% decrease in failure rates during testing phases.
Another compelling example involves a global automotive company that had struggled with ensuring that their components met reliability standards before they went into mass production. By incorporating Windchill Reliability Prediction into their workflow, the engineering teams were able to conduct predictive analyses on component longevity and performance. This proactive approach enabled them to identify potential failures earlier in the design process, significantly reducing warranty claims and enhancing customer satisfaction. The company noted a 40% reduction in post-launch defects, demonstrating the effectiveness of predictive reliability insights in achieving engineering excellence.
In the technology sector, a prominent electronics manufacturer adopted Windchill to streamline their product lifecycle management. This implementation allowed them to forecast reliability issues based on historical data and current design configurations, enabling data-driven decision-making in their design processes. By leveraging Windchill’s predictive capabilities, they improved their product reliability ratings and accelerated their time-to-market by 15%. These case studies provide evidence that implementing Windchill Reliability Prediction delivers measurable benefits, offering engineering executives a blueprint for optimizing their design and production strategies.
Best Practices for Implementing Windchill Reliability Prediction
Implementing Windchill Reliability Prediction effectively can significantly enhance an organization’s engineering capabilities. To achieve optimal integration of this software, it is crucial to employ best practices that align with existing processes while fostering a collaborative environment among team members.
First, a thorough assessment of current workflows and systems is essential. Understanding how Windchill Reliability Prediction can complement these processes will help in creating a seamless integration plan. Identifying key stakeholders and involving them early in the implementation process can lead to better alignment and smoother transitions. It’s advisable to map out a clear strategy that highlights specific objectives, timelines, and measurable outcomes. This structured approach will facilitate tracking progress and ensuring accountability among team members.
Another critical aspect is securing buy-in from the team. Engaging employees in discussions about the benefits of Windchill Reliability Prediction is vital for fostering a positive attitude toward the software. Conduct training sessions to enhance their understanding of its functionality, thereby alleviating any apprehensions surrounding its adoption. Continuous support from leadership and open communication channels can bolster confidence, ensuring that users feel valued and empowered.
Additionally, it is important to leverage the full potential of Windchill Reliability Prediction by customizing its features to fit specific organizational needs. This may include adjusting metrics to align with specific project requirements or incorporating data analytics to monitor performance effectively. Regularly soliciting feedback from the users will help in identifying areas for improvement, ensuring that the tool remains relevant and useful.
Ultimately, implementing Windchill Reliability Prediction is not just about technology adoption; it’s also about nurturing a culture of reliability and continuous improvement through integration, engagement, and optimization.
Future Trends in Reliability Prediction
The landscape of reliability prediction is rapidly evolving, with significant advancements in technology that promise to enhance the capabilities and applications of tools such as Windchill. One of the most notable trends is the integration of artificial intelligence (AI) and machine learning into predictive analytics. These technologies are enabling the development of sophisticated algorithms that can analyze vast amounts of data, identifying complex patterns and anomalies that traditional methods might overlook. As engineering executives increasingly leverage these models, they can expect more accurate and timely predictions regarding product performance and reliability.
Another emerging trend is the use of the Internet of Things (IoT) in reliability prediction. By utilizing sensors embedded in products and systems, real-time data can be collected about performance, wear, and environmental conditions. This data can then be processed using AI algorithms, enhancing the predictive maintenance capabilities offered by systems like Windchill. As a result, organizations can transition from reactive to proactive maintenance strategies, leading to improved uptime and reduced operational costs.
Moreover, the application of big data analytics continues to gain traction in reliability prediction. By harnessing large datasets from various sources, including customer feedback, warranty claims, and historical performance data, engineering teams can conduct a more comprehensive analysis. This holistic approach ensures that predictions are based on a wider context, ultimately contributing to better decision-making. Additionally, cloud computing platforms facilitate the storage and processing of this vast data, making it accessible for predictive analysis at any time and location.
As we look to the future, the intersection of AI, IoT, and big data analytics with reliability prediction through tools like Windchill presents engineering executives with unprecedented opportunities. Embracing these advancements will not only enhance product reliability but also support strategic objectives, enabling organizations to stay ahead of market demands.
Conclusion: The Path Forward for Engineering Executives
In conclusion, the role of Windchill Reliability Prediction is becoming increasingly pivotal for engineering executives as they navigate the complex landscape of modern engineering challenges. This predictive tool provides invaluable insights into product reliability and performance, enabling decision-makers to plan strategically and allocate resources effectively. Engineering executives who integrate Windchill Reliability Prediction into their workflows gain a comprehensive understanding of potential pitfalls and successes, ultimately making informed choices that enhance productivity and innovation.
The capabilities offered by Windchill Reliability Prediction empower executives to mitigate risks associated with engineering projects. By accurately forecasting potential failures and maintenance needs, executives can optimize their scheduling, reduce downtime, and streamline processes. As a result, organizations can achieve greater efficiency and maintain a competitive edge in the marketplace. The data-driven nature of this predictive capability also supports the establishment of KPIs and performance benchmarks, assisting executives in evaluating progress and adjusting strategies as necessary.
Moreover, the integration of Windchill Reliability Prediction fosters a culture of continuous improvement within engineering teams. By encouraging engineers to rely on predictive analytics, organizations can promote open communication and collaborative problem-solving. This holistic approach ensures that all team members are aligned with the company’s objectives, ultimately leading to heightened morale and job satisfaction.
As the engineering landscape continues to evolve with advancements in technology and shifting market demands, the importance of utilizing tools like Windchill Reliability Prediction cannot be overstated. Engineering executives must leverage these resources to remain agile, informed, and responsive to new challenges. By committing to this path forward, they will not only enhance their operational efficiency but also pave the way for sustainable success in their organizations.